両面加工でつくる、最速のホイール
本記事では、両面加工を駆使し、最速を実現するホイールとギアの一体化パーツの製作方法をご紹介します。
今回の動画で使用したもの
- 機種 :KitMill CL200
- CAM:Cut2D
- 刃物 :汎用超硬スクエアエンドミル(Φ0.5、Φ4)
- 材料 :ポリアセタール板(POM)T=15mm(黒)、T=5mm(白)
ズレのない両面加工を施すための、基準ピンを用いた位置合わせ
ズレのない両面加工を行うためには、表側の加工後、材料を裏返した際に正確な位置合わせを行う必要があります。 今回は、治具用材料・材料に穴加工を施し、位置決めの基準となるピンを打ち込むことで材料の位置合わせを行う方法をご紹介します。
1. NCプログラムの作成
NCプログラムの作成には、「Cut2D」を使用しました。「Cut2D」には両面加工に対応する便利な機能が標準で搭載されています。
1-1 | 表側の図形データを読み込み、「両面」を選択します。Zゼロ位置の項目は、「素材サーフェス」を選択します。素材の反転方向は、加工に合わせて任意に選択します。(今回は、X軸回転方向で加工を行いました。)
1-3 | 表、裏それぞれのツールパスを作成します。
工具経路プレビューで「全ての面をプレビュー」を選択すると表側、裏側の加工結果が表示されます. ます。両面の加工結果が表示されますので、作成したNCプログラムにズレが無いかを確認することができます。
■ 基準ピン用の穴は、加工範囲の中心線から等距離の場所に2つ以上あけます。治具に基準ピンを打ち込んだ際にぐらつかないように、材料を貫通させ、治具用材料の表面から3mmの深さまで穴加工します。
■ CAMによって両面加工の際の反転方法が異なるため、基準ピン用の穴の位置はCAMに合わせる必要があります。今回は、X軸回転方向で加工を行いました。
4-3 | 材料の表側に固定用の両面テープを貼り付けます。材料の固定は基準ピンに打ち込んだ後、クランプで行うことも可能です。
4-4 | 材料を裏返し、基準ピン用の穴と基準ピンの位置を合わせ、はめ込んで固定します。
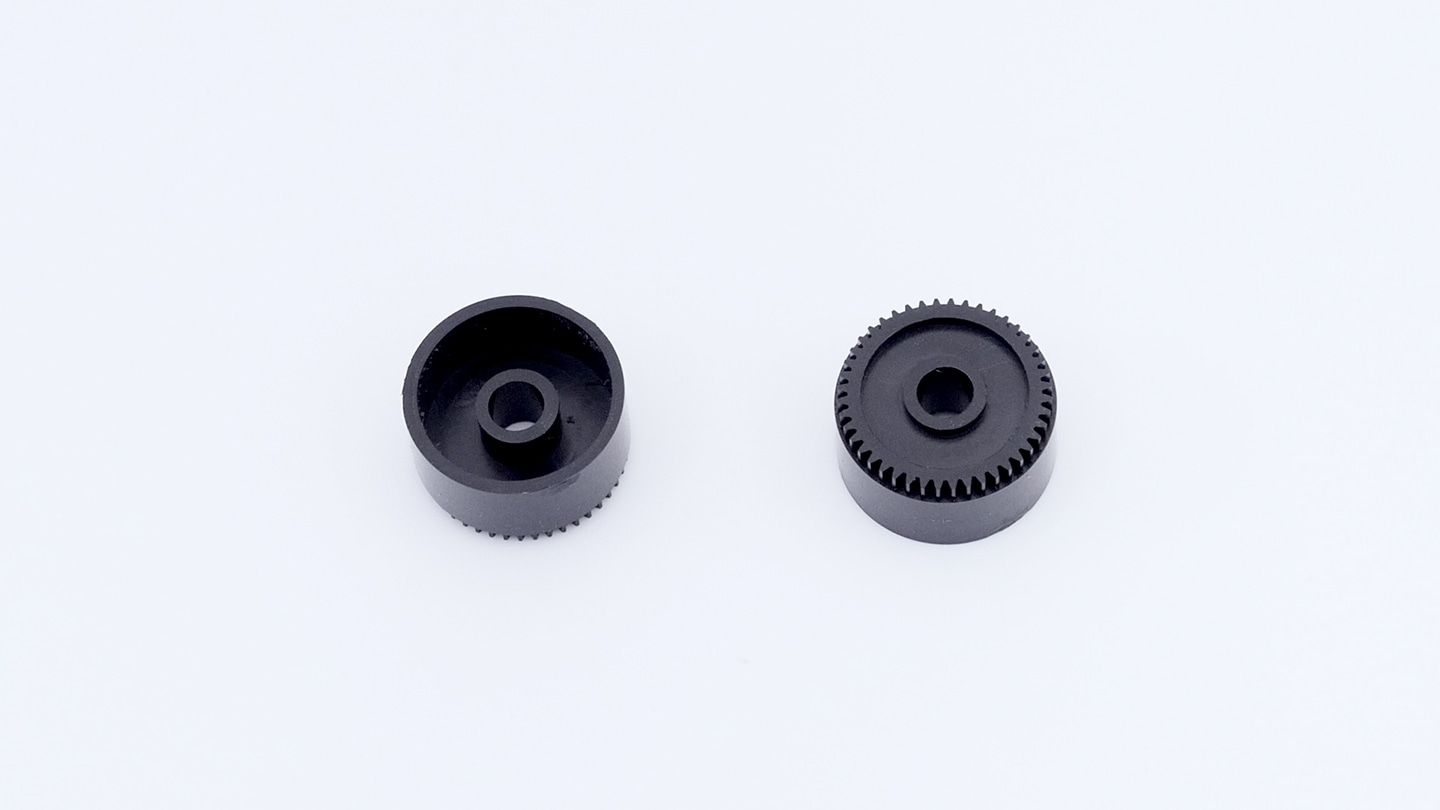
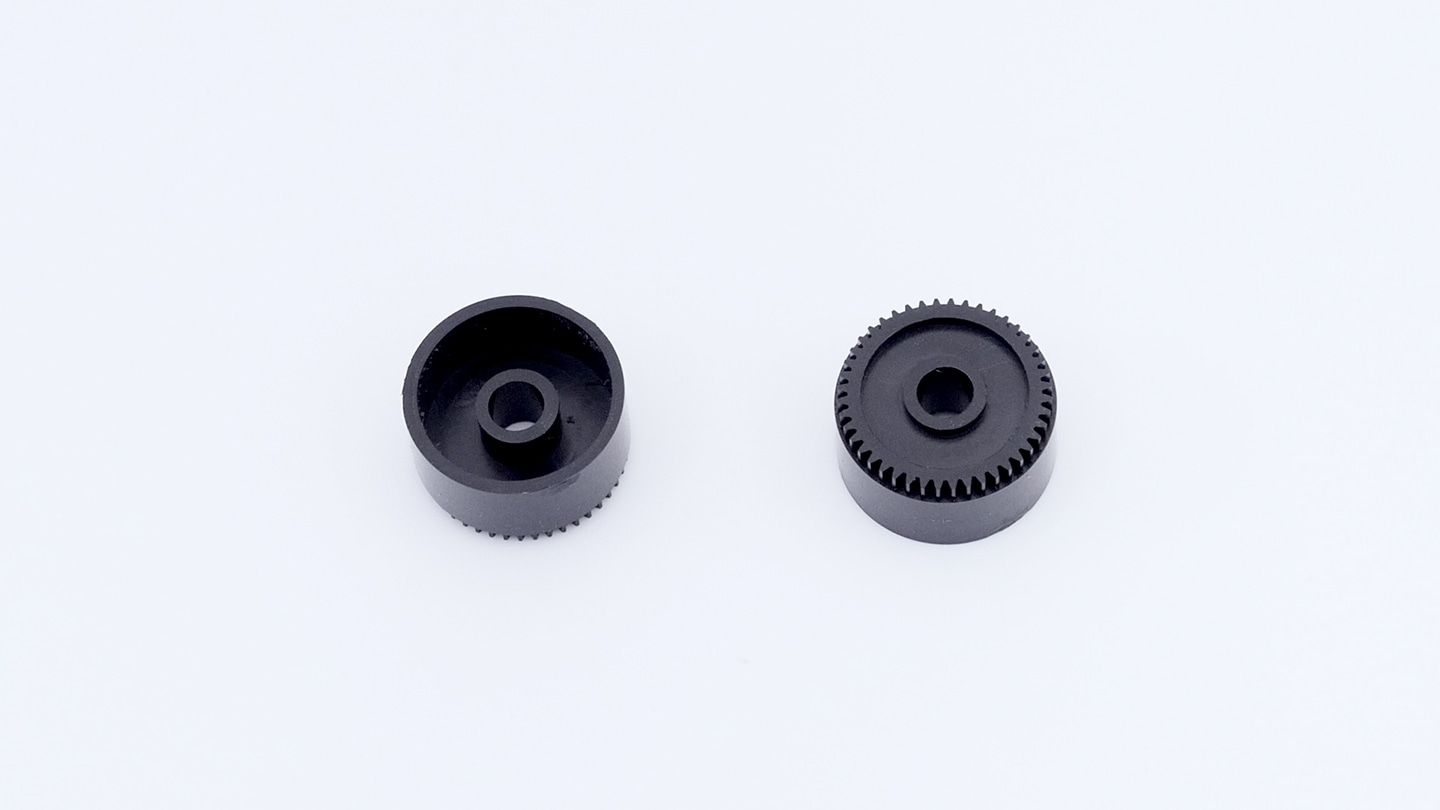
材料からパーツを切り離し、バリ取りをしたら加工完了です。
関連記事
Sample Collection KitMill / 繊細でなめらかな質感を持った、木製カトラリー。
「KitMill」で両面加工を施し、繊細でなめらかな質感を持った木製カトラリーを制作しました。切削加工は木材の美しい木目や、優しい肌触りを活かした作品を製作することができます。
「Cut2D」を用いた「KitMill」で使用できるNCプログラムの作成方法をご紹介します。
自分で組み立てられるキット式のデスクトップ型CNCフライス「KitMill」シリーズの使い方。こちらでは見本として「KitMill CL100」を用いて、アルミ板を切削加工する場合の流れをご紹介します。