KitMillの歴史
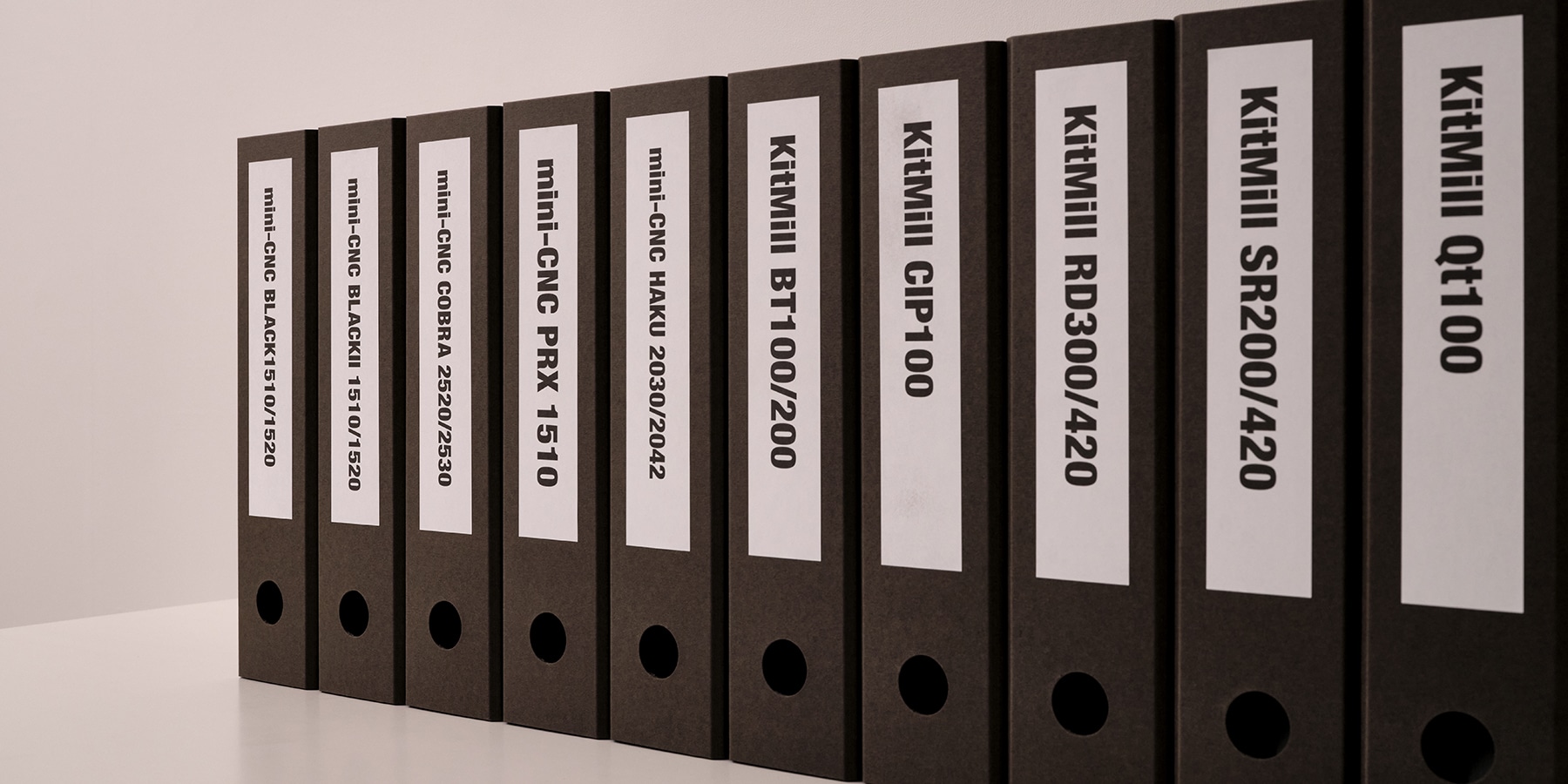
私たちのデスクトップ型CNCフライス「KitMillシリーズ」は、最終製品だけを見ると、初めからそのような形や機能を備えていたかのように見えるかもしれません。しかし、どの機種においても開発当初はそれとはかけ離れたものであり、発売に至るまでには数多くの苦難苦闘を乗り越えてきた歴史があります。ここでそれらを紐解いてみたいと思います。
【第一部】孤高の開発者の苦闘と初号機「mini-CNC」(2003年~)
当社が初めて「デスクトップ型CNCフライス」を製品化したのは2003年です。そのきっかけは、2002年の秋に私がインターネットで見つけた、基板加工機を自作している人たちの製作記事でした。基板加工機とは、銅箔が貼り付けられた「生基板」と呼ばれる板材の表面を切削することで配線パターンを作っていく機械のことです。当時の私が知る基板加工機は、主に大学や企業の研究室に導入されている高価な機械で、とても個人で購入して利用できるものではないという印象でした。ところがその機械を自作している人がいることを知り、私はとても衝撃を受けました。
当時はエッチング液による基板製作もよく行われていましたが、うまく露光できなかったり、廃液処理が面倒だったり、同じ品質の基板を複数作ることが難しかったりと、さまざまな問題がありました。また、今では個人でも基板製作を外注しやすくなりましたが、当時は個人が外注など考えられもしない時代でした。ですから、これをキット化して個人のお客さんのために販売すれば喜ばれるのではないかと考えたのです。同時に、「自分がやらなければ誰がやるのだ」といった使命感にも似た気持ちも持っていました。
しかし当時は、低価格な中国製品が広く出回りはじめた時代です。そのせいか、わざわざ自作するよりも出来たものを買ったほうが安いし手っ取り早いからと、自作する人がどんどん減っていきました。電子工作関連の雑誌も次々と廃刊となり、唯一自作文化の残っていたパソコンでさえ自作する人が減少していったのです。ですから、「そんなことをやっても商売にならない」と人によく言われたものでした。だからこそ私は、「自分がやらなければ誰がやるのだ」といった使命感のようなものを感じたのかもしれません。
開発にはいろいろな困難が伴いました。当社はその頃、私たった一人の会社で人脈も少ない上に取引金額も少額でしたから、納期が後回しにされてしまったり、不良品が納品されてもすぐに対応してもらえなかったりといったことが頻繁に起きました。
開発資金にも困りました。社員という立場での開発業務であれば、仮にその開発が失敗しても給料をもらうことができます。しかし私は独立した個人事業者です。誰も私の面倒を見てはくれません。資金を確保するため、当時の主な業務であったソフト開発の仕事をこなしながら開発を進めていきました。実に毎日朝7時半から深夜2時ごろまで、さらに土日も休むことなく働き続けました。
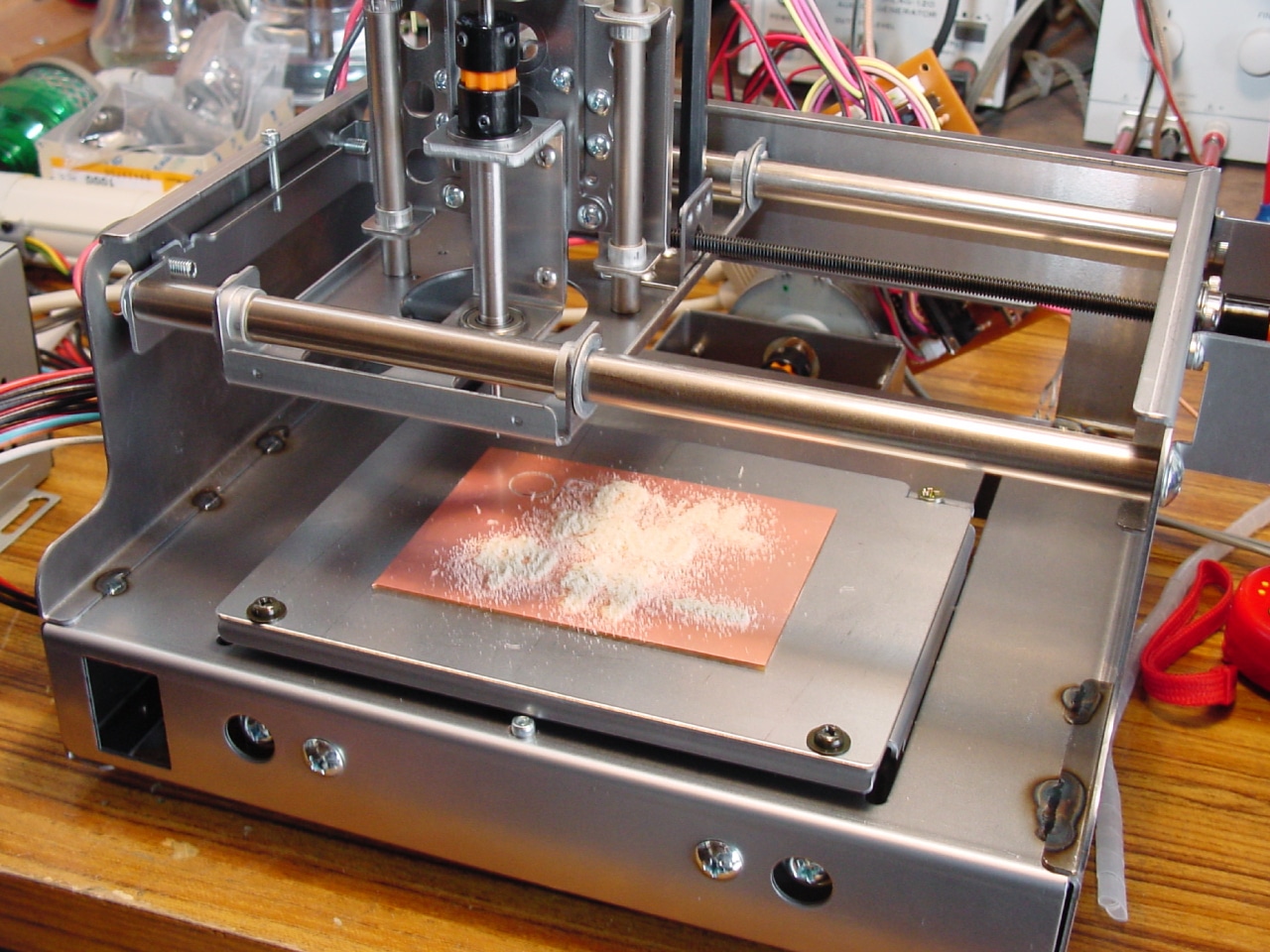
▲ mini-CNC 試作第一号機(2003年2月頃)。加工テストをしてみたところ、基板だけではなくアルミも加工できることがわかった。それ以降は、基板加工機ではなく、アルミも加工可能なCNCフライスとして開発を進め、名称も「mini-CNC」と決めた。
mini-CNCは、フレームに板金を使ったり、その板金にブッシュを打ち込んだり、送りねじに全ねじを使ったりといった工夫をしているのですが、実はこれはとても勇気のいることなのです。そのような工夫は産業機械の設計者としてはかなり非常識な行為だからです。もちろんフレームに鋳物を使い、高精度なリニアガイドやボールねじを使えば良いものが作れることはわかっています。でも、それでは個人に手が届く値ごろ感のある製品にはなりません。「個人向け」という強烈な制約の中で、必要な機能と性能を満たすには常識を超えた創意工夫がどうしても必要だったのです。まさに、つくり手の実力が試されるところでした。
さらに、「メカ系の組み立てキット」という文化の種すらない頃ですから、ビジネスモデルも構築しなければなりませんでした。組み立てキットは文字通りお客様が組み立てるものですから、部品をバラバラの状態でお送りすることになります。それをどのようにして梱包すべきなのか。梱包箱の構造が一般的な製品よりもかなり複雑になります。また、組み立てやすさにも配慮しなければなりませんし、取扱説明書にも手順の詳細な図解が必要です。さらには、保証や法令遵守、安全確保、サポートなどの方法が一般的な製品とは大きく異なるのです。
当時は私の調べる限り、メカ系の組み立てキットを作っている企業など国内には一社もありませんでした。「前例のないビジネス」といえば聞こえが良いのですが、参考となるビジネスモデルが何もないのです。今となっては当たり前のように思えることでも、一つひとつを決めていくことは、想像以上に苦しく大変なことでした。
それでも困難をなんとか乗り越え、7回の試作を経て、ついに2003年9月、オリジナルマインドの初代CNCフライス「mini-CNC」は発売されました。
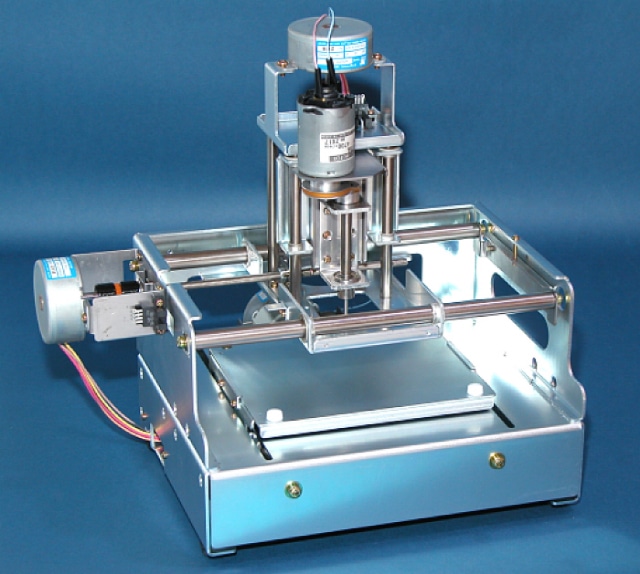
▲ 初代mini-CNC。半年後に本体色を黒にして名称を「mini-CNC BLACK」としたが、発売直後の本体色はシルバーだった。
私は一台あたりの販売価格を下げるために、たくさんの台数を生産していました。一度に数百万円のお金が出ていったわけです。個人にとって数百万はとてつもなく大きい金額です。ですから「もし売れなかったらどうしよう」という強烈な不安を抱えていました。そしてやはり、発売当初は思うように売れませんでした。田舎の無名のメーカーがアクセスの少ない自社サイトで販売してもなかなか売れないのは当然です。
ところが、2004年5月頃になると、急激に売り上げ台数が伸びていきました。なぜこんなに売れるのか。しばらくその理由がわかりませんでした。調べてみると、mini-CNCは二足歩行ロボットの製作に利用されていたのです。当時、ロボットの製作ブームが起きており、中でも2002年に始まった二足歩行ロボット大会「ROBO-ONE」は大変な盛り上がりでした。やはり二足歩行ロボットというのは人間と同じ動きをしますから、目を惹きつけますし、テレビでも話題になっていたのです。このため、そのROBO-ONE大会に出場するロボットクリエイターがたくさん現れてきました。
二足歩行ロボットを作るには、そのパーツに「カッコよさ」を演出するための美しい曲線や、軽量化のための肉抜き、精度の高い穴などが必要になります。mini-CNCは、そうした複雑な形状の部品を精度よく、しかも自動でいくつも加工できるため、まさにロボット製作に打ってつけでした。そして、その火付け役になったのが神奈川県に住む井上裕二さんでした。井上さんは自身のブログでmini-CNCを紹介してくださり、それを見たロボットクリエイターたちが、同じようにmini-CNCを利用してくださるようになったのです。さらに、mini-CNCに「黒い奴」というあだ名をつけてくださったため、当時のロボットクリエイターたちの間では、その愛称で呼ばれるようになりました。
いまもそのサイトがそのままに残されています。
その後、「黒い奴」に引き続き「mini-CNC COBRA」「mini-CNC HAKU」と機種を増やし、いつしか「mini-CNC」という名称は製品名という枠を飛び越えて、ユーザーがデスクトップ型CNCフライスを指す代名詞となって広く知られていきました。
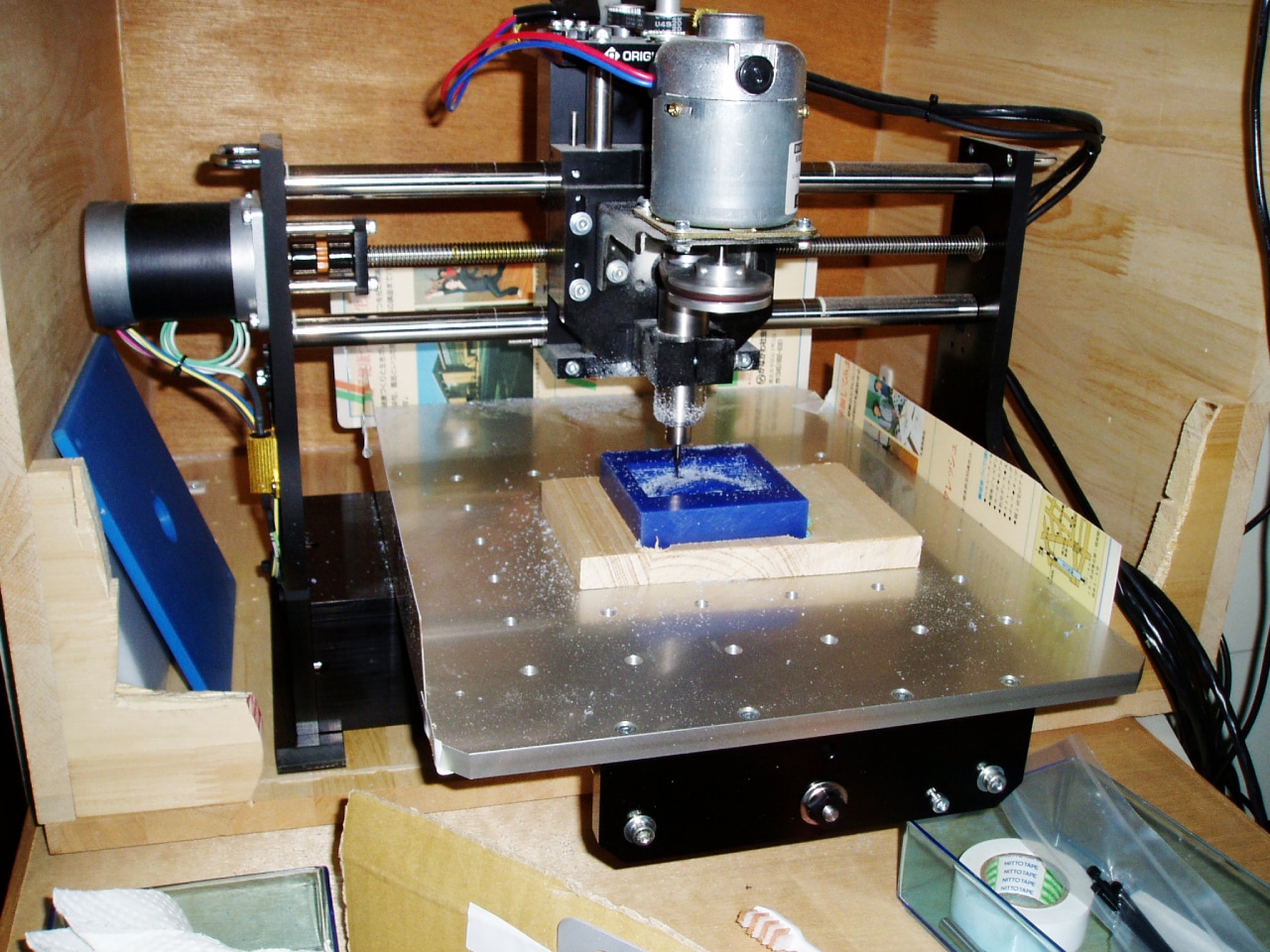
▲ mini-CNC COBRA 2520の試作第一号機。当初はリニアブッシュで構成されていたが、剛性不足によりリニアガイドに変更した。また、このクラスになってくると、それまでの定電圧方式のドライバでは性能が発揮できないため、新たに定電流方式のドライバ(QUATTRO-1)を開発。着手から発売まで二年もの期間を要した。
【第二部】新たなシリーズ「KitMill」と若手開発者の挑戦(2010年~)
mini-CNCは多くのつくり手たちに支持され、広く市場に浸透していきました。同時にmini-CNCという名称もまた、製品名という枠を超えてデスクトップ型CNCフライスの通称として広く浸透していきました。これほどまでに浸透したことは本当に嬉しかったのですが、mini-CNCという名称は商標登録をしていなかったために、他社からmini-CNCを冠した製品が登場してきてしまったのです。このため私は、名称を変更するとともに、シリーズを刷新させる必要性を感じ始めていました。
おかげさまでこの頃には社員も増えて、製品開発は私の手を離れ、若手社員たちの手で行われはじめていました。そこで、このmini-CNCを今後どう発展させるかをみんなで話し合い、コントローラーの新規開発と加工性能の向上を行うことにしました。
まず、新規開発するコントローラーはUSB接続に対応することにしました。mini-CNCはもともとパラレルポート接続しか対応していませんでしたが、パラレルポートを搭載したパソコンは次第に少なくなってきたため、USB接続への対応は必須課題でした。
パラレルからUSBへの変更は、一見簡単なことのように思えるのですが、実は大きな技術的課題があります。ステッピングモーターを動かすにはパルス信号が必要だからです。パラレルポートは文字通りパラレルですからパルス信号を同時にいくつも出力できるのですが、USBはシリアルポートですから同時に1つの信号しか出力できません。信号変換だけでは解決できないため、制御方式をすべて別のものに変える必要がありました。
当初私たちは「USBCNC」というコントローラーを海外から取り寄せ、それを使用することでこの問題を解決していました。しかし、その方法ではコントローラーとドライバが別々になっているため、配線も複雑になります。そこで、構成をもっとシンプルにして扱いやすいコントローラーを新規開発しようということになりました。
完全オリジナルなコントローラーを開発することも検討しましたが、試算したところ膨大な時間と費用がかかることがわかりました。開発にかかる時間や費用は製品価格に上乗せざるを得ません。自社ブランドに憧れはありましたが、ユーザーに求められているものは何かを考え直し、別の方法を取ることにしました。それは、「USBCNCのCPUのみをライセンス購入し、それをドライブ基板に搭載することで、シンプルに一つにまとめる」という方法です。USBCNCはすでにユーザーに受け入れられていましたから、これなら移行もスムーズです。また、USBCNCは海外メーカーの製品でしたが、すでに取引実績があり信頼関係も構築できていたため、設計データも提供していただくことができたのです。こうして、それまで別々だったコントローラーとドライバを一体化した「TRA100/150」が誕生したのでした。
▲ mini-CNCシリーズ時代の接続イメージ
▲ KitMillシリーズの接続イメージ
それと並行して、加工性能向上も進めました。当時売れ筋だった「mini-CNC HAKU 2030/2042」は、複数の部品を一度の加工で削り出すのに最適な広い作業領域と、30万円を切るコストパフォーマンスの高さが魅力でした。その長所を生かしながら剛性と減衰性の両方を高めることを目標に、性能向上を検討しました。
以前と違って、この頃にはある程度の販売台数を見込めるようになっていたため、検討にあたっては、金型などイニシャル費のかかる製造方法や海外生産も選択肢に入れました。最終的には、鋳鉄とアルミ押し出し材を主なフレーム材として採用することになったのですが、この結論に至るまでには、厚板やアルミ鋳物を使った実験を繰り返し、調達先の確保をめぐって海外や国内の製造業者との交渉を何度も行うなど、たいへんな苦労が伴いました。
その経緯についてお話ししますと、当初行っていたアルミ鋳物のベースを使っての実験では、剛性不足で振動が出てしまい安定しないため、次にベースを削り出しの鉄に変えて実験しました。それによって剛性は向上したものの、どうしても機体の振動が消えません。そこで鋳鉄ベースの案が浮上しました。
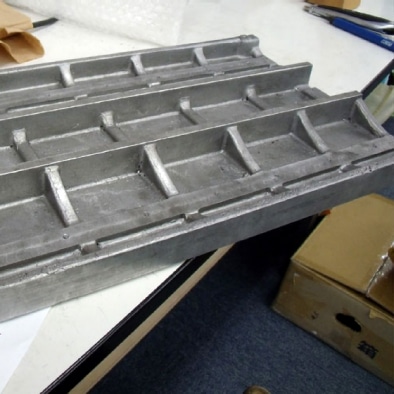
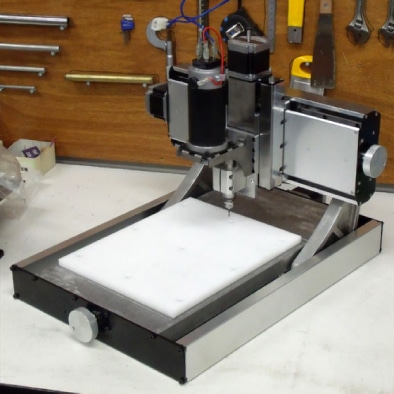
▲ 左:アルミ鋳物製ベースの試作品。 右:そのアルミ鋳物製ベースを使った第一次試作品。振動が出てしまい安定しなかった
鋳鉄はその成形の過程で内部に小さな黒鉛が散りばめられるために、これが絶妙なクッションとなり機体の振動を吸収してくれます。試しに鋳鉄の定盤に穴を開けてフレームを立てて実験してみたところ、確実に減衰性が大幅に向上し振動も収まったのです。効果を確認できたことで、HAKUの後継機では鋳鉄製ベースフレームを採用することが決まりました。
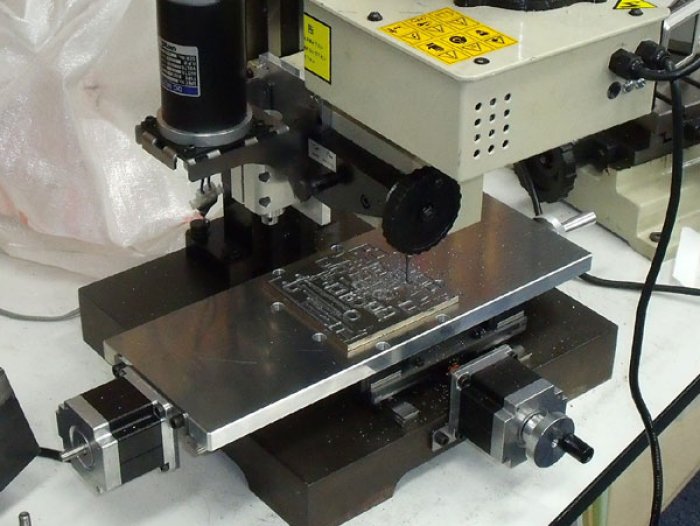
▲ 鋳鉄の定盤に穴をあけフレームを固定して実験。減衰性が大幅に向上し振動も収まった。
しかし問題はここからでした。鋳鉄が固まる過程や加工を施した際に変形が発生してしまったり、湯口の位置によって形が崩れてしまったりと、これまで経験したことのない様々なトラブルに見舞われたのです。鋳鉄は減衰性に優れている反面、型を使用して成形をするために後から設計の変更ができません。切削部品のように精密な寸法で成形することもできません。このため、型を作り直しては検証をするという繰り返しを何度もせざるを得ず、その開発費と期間は膨大になっていきました。
調達先の確保にも苦労しました。国内では高い技術を持つ鋳物工場が減少してきており、製品イメージに合った鋳肌を実現していただける調達先がなかなか見つからなかったのです。加えて、「コストパフォーマンスの高いHAKUの後継機」という前提での、コストと品質の調和という課題もありました。そこで中国の鋳鉄メーカーを探して現地へ赴き、何度か試作をお願いしました。ところがコスト面では満足できたものの、品質の均一性が保てず、ついにそれが解消できなかったのです。
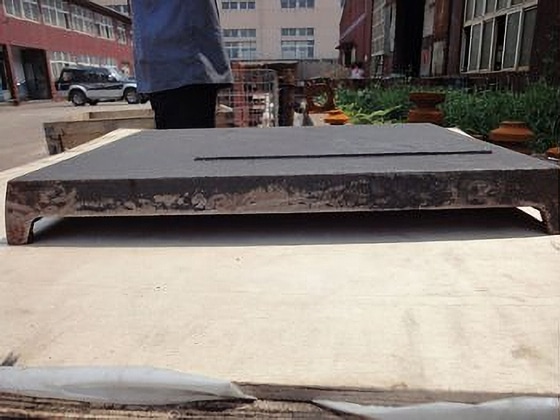
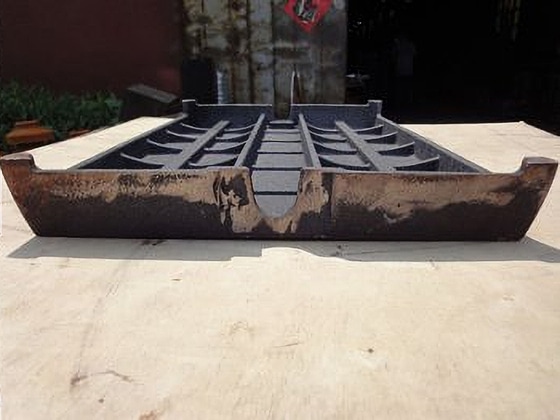
▲ 中国で製造してもらった鋳鉄ベース
コストはもちろん大切ですが、私たちはお客様が所有することに対して誇りを感じてもらえるほどの製品を作りたいと考えていました。その後は品質最優先で調達先を探し続け、ようやく高い技術を持つ鋳物鋳造をしていただける業者と出会うことができました。その結果、本来のイメージ通りの品質を実現することができました。
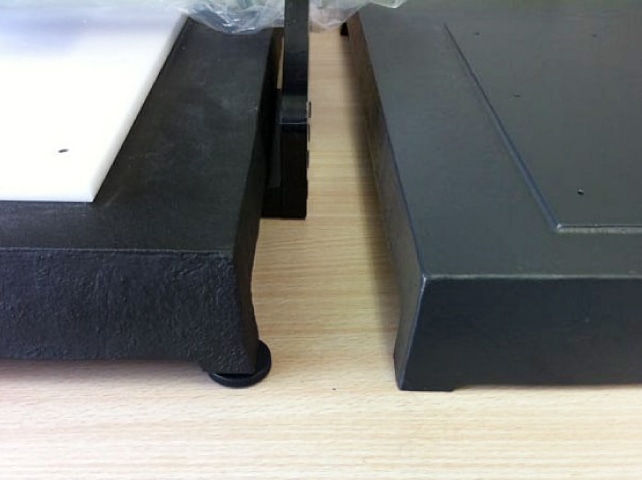
▲ 左:中国製鋳鉄ベース、右:国内製鋳鉄ベース
しかし、品質にこだわり続けた結果、その原価は想定よりかなり高くなってしまい、それに伴って販売価格も上げざるを得ず、HAKUの後継機という位置づけも解消せざるを得ませんでした。また、長い時間と費用をかけて試作と検証を繰り返してきたものの、そもそも鋳物を利用した個人向けのCNCフライスなど他にはなく、こういった製品がユーザーに受け入れられるかは発売してみないとわかりません。ですからこのときも、期待と不安が半々な状態での発売となりました。それが当社初の鋳鉄製ベースフレームのCNCフライス「KitMill RD300/420(のちのKitMill RZ300/420)」です。
これら新製品の誕生に合わせて、当社のCNCフライスシリーズの名称を「mini-CNC」からすべて「KitMill」へと改め、これを商標登録しました。多くのユーザーに「黒い奴」と呼ばれ愛されてきた「mini-CNC BLACK 1510/1520」も、剛性と組み立てやすさを向上させて「KitMill BT100/200(のちのKitMill BS100/200)」としてリニューアルしました。これが2011年のことです。
続いて、フル鋳鉄フレームのハイエンドモデル「KitMill AST200」を発売しました。これは、「KitMill RD300/400」で得たノウハウや教訓を活かしての開発となりました。
「KitMill AST200」は、加工性能の高さが大きな特長となっていますが、それ以外のところにも実に多くのエネルギーがかけられています。それは、「所有するよろこび」「削るよろこび」とも言うべきものが、これまでの製品で最大になるように考え抜いたことです。
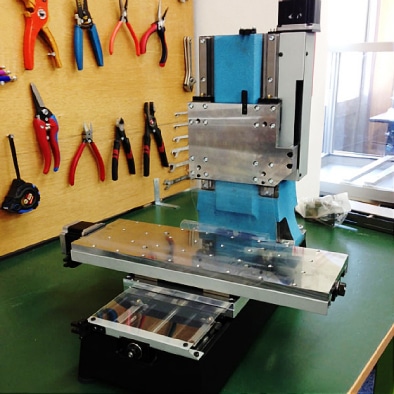
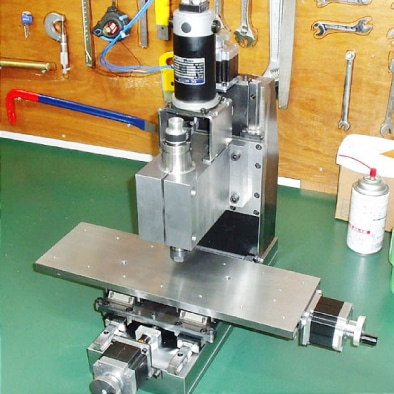
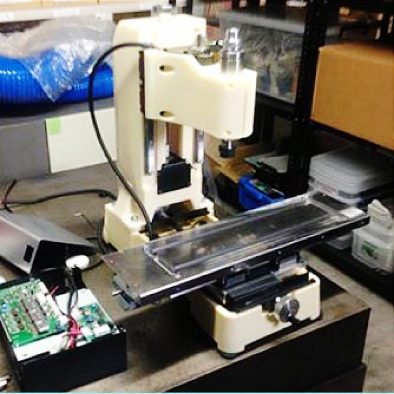
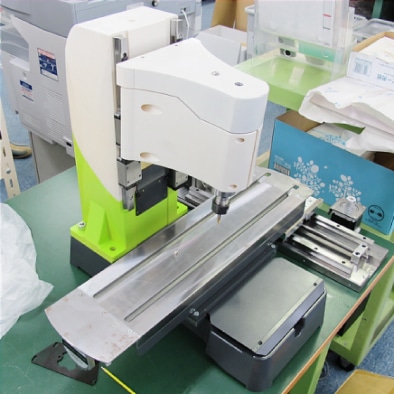
▲ AST200の試作品。そのシンプルな姿からは想像しがたいかもしれないが、AST200の開発は膨大な手間と費用がかさみ、苦難苦闘の連続だった。開発期間は3年にも及んだ。
私たちはそうした数値化できない価値のことを「感性価値」と呼んでいるのですが、こういったことには正解がなく、人によって感じ方も異なりますから、技術的な難しさとはまた違った難しさがあります。プロダクトデザイナーの方に相談したこともあったのですが、あまりうまくいきませんでした。というのも、私たちの製品は限られたコストの中で最大限に性能を発揮させるため、装飾だけを目的とした部品はひとつもなく、構造的に役に立っている部品だけで美しさを表現しています。このため、外観だけ考えれば良いというわけではなく、設計や製造の知識が必要になります。そういったことまで考えることのできるデザイナーの方はなかなかいるものではありません。結局「自分たちでやるしかない」ということになり、開発者が主体となって考え、それと合わせて技術的な課題も解決していきました。このときの経験は、以降の製品開発にも大きな影響を与えています。
【第三部】3Dプリンタの出現と木工CNCの誕生(2013年~)
2013年頃になると、3Dプリンタが出現し急速な勢いで普及していきました。その勢いは驚くほどで、技術系の展示会に行くと、3Dプリンタを展示するブースはいつもたくさんの人でごった返していました。ほどなく家電量販店の店頭で取り扱われるほどの小型・軽量でお手頃価格の機種も続々と現れ、「なんでも作れる魔法の箱」として華々しく取り上げられたり、さらには、それを使って銃をつくる人が現れ、ニュースにもなったりしました。そうして「3Dプリンタ」は、あっという間にペンチやドライバと同じぐらい誰もが知る工作ツールとなっていきました。同じ工作ツールでも、いまだに認知度の低い「フライス」とは大違いです。
私たちは、3Dプリンタのあまりの人気ぶりに、「もしかしたらKitMillは売れなくなってしまうのではないか」という不安を感じていました。KitMillと3Dプリンタは「切削式」か「積層式」かの違いだけで、どちらも立体形状を作るための装置だからです。そして実際、KitMillの売り上げは少しずつ低迷していきました。
このため、一時は3Dプリンタ市場に参入することも考えました。お客様からも「オリジナルマインドも3Dプリンタを出すのではないか」という声がSNS上にしばしば上がりました。しかし社内での長い議論の末、「CNCフライスの開発で長年培ってきたノウハウは、CNCフライスの性能を高めていくために活かすべきだ」という結論にまとまりました。それと同時に、「切削加工ならでは」の製作物をつくることができる新たな機種を開発することを決めました。
切削加工には大きな特長があります。それは「素材の特性や見た目の持ち味を活かすことができる」という点です。たとえば、木目調の美しい楽器や、ぬくもりを感じる家具などは、3Dプリンタではつくることができません。その発想から生まれたのが、木工専用CNC「KitMill MOC900」です。テーブルサイズはKitMillシリーズの中で最大の750mm×1200mm。椅子やテーブルといった実用的な家具はもちろん、人が乗り込むような大きな作品づくりも可能になりました。
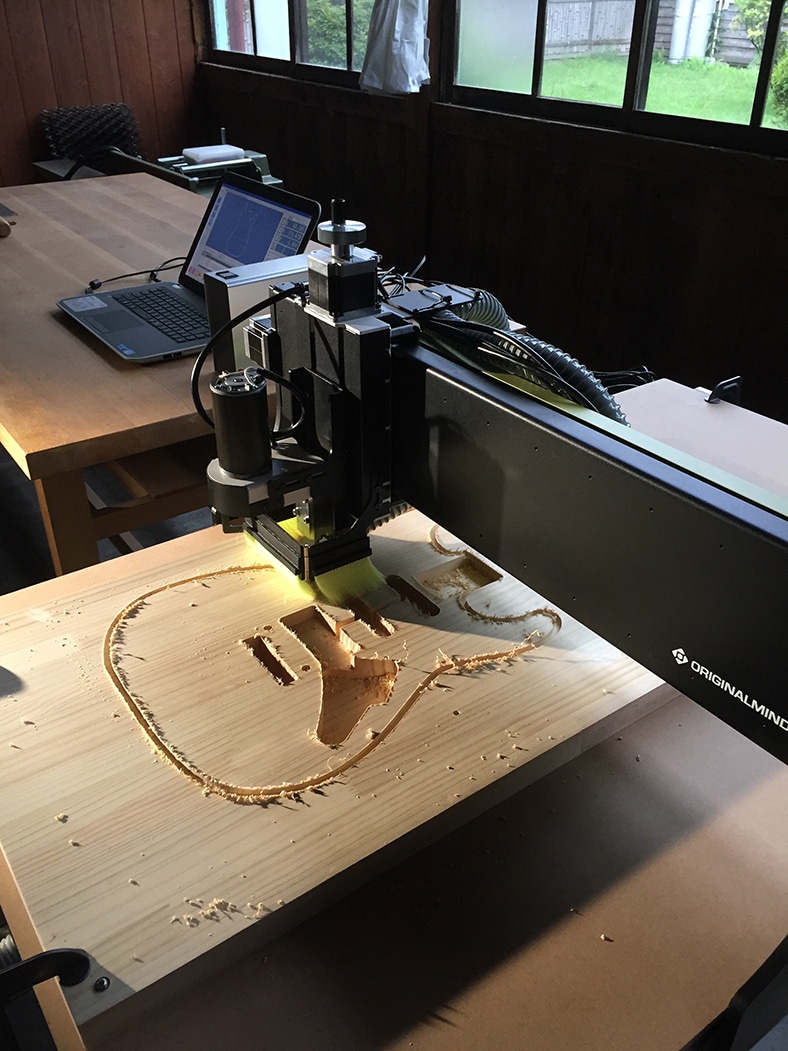
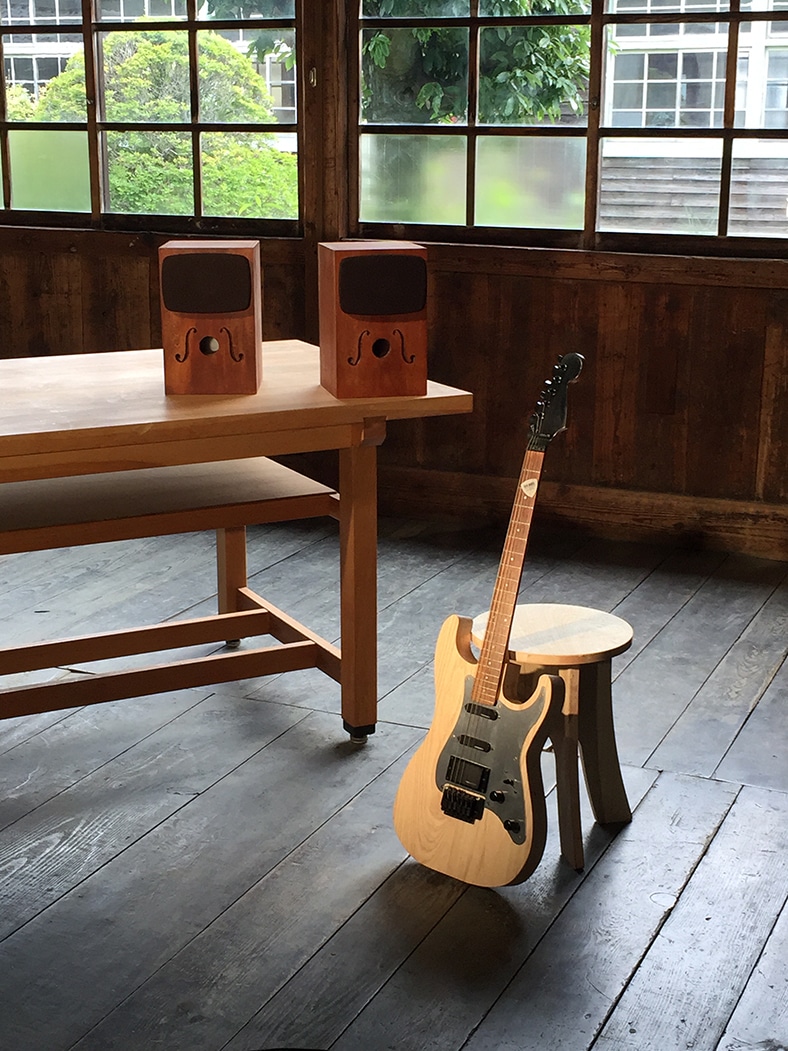
▲ KitMill MOC900によるギター加工のようす
3Dプリンタの出現により落ち込んでいたKitMillの売り上げは、翌年から少しずつ回復していき、2015年には、むしろ3Dプリンタブームが発生する前よりも伸びていきました。その理由は、「MOC900の売り上げが上乗せされたから」と言いたいところですが、実はそれよりも大きな理由があります。3Dプリンタの導入を出発点として加工を楽しむようになったお客様が、工作範囲を広げていくにつれて、KitMillを必要としてくれるようになったからです。さらには無料の3D-CADの普及や、あらゆる形状の3Dデータがネット上にたくさん載せられるようになったことも追い風となりました。3Dプリンタの普及は私たちにとって敵どころか味方になってくれたのです。
それだけではありません。「メイカームーブメント」と称される個人のものづくりがだんだんに盛り上がり、全国にFABスペースが次々と開設されました。KitMillを設置して下さる施設もたくさん現れ、まるで全国に私たちのショールームができたような状況になり、そのおかげでKitMillはこれまで以上に広く全国に普及していきました。気が付くと、KitMillは全国の工業系大学のほぼ全てに導入されるというほどまでに普及していました。
【第四部】これまでのノウハウを結集させたKitMill CL100/200/420(2017年~)
2003年の発売以来、KitMillはお客様のニーズや用途に合わせてラインナップを充実させてきました。しかしお客様から「この機種とこの機種の違いは何ですか?」というご質問をよくいただくようになりました。機種が増えたことで、選定に迷いと混乱を生じさせてしまっていたのです。
また、私たちは即日発送を徹底しているということもあって、抱える在庫量が膨大になり問題になっていました。在庫過多は経営を圧迫します。それに、会社というのはお客様からいただく利益で成り立っていますから、あらゆる費用は販売価格に上乗せせざるを得ません。そうなると、お客様に負担を掛けてしまいます。
このため、社内で話し合いを行い、ラインナップを見直すことにしました。そこで決まったことは、CIP100、SR200/420、Qt100の3機種を1つの機種に統合しようというものでした。こうすれば、各部品の1ロットあたりの製作数が増え、量産効果により製造原価が下がります。在庫や管理の負担も減るので、販売価格を抑えることができます。さらに、他の機種と仕様や用途に重複がなくなり、選定もしやすくなります。こうして2018年に開発をスタートさせたのが、KitMill CL100/200/420です。
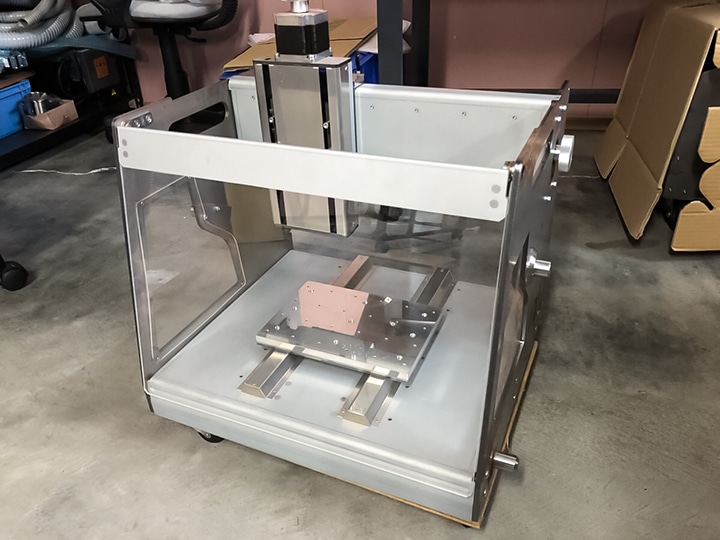
▲ CLの試作第1号機。最終製品からは想像できないが、当初はカバー付きの一体型を検討していた。
CLでは、前機種のQt100とSR200/420の加工範囲を1機種でカバーするために、CL100、200、420の3サイズをご用意し、目的や用途に応じて加工範囲を選択できるようにしました。また、X軸の構造を以前の横型から縦型に変更することで、本体剛性を高めるとともに、広い加工範囲を持ちながらも外形サイズがコンパクトになるよう設計しました。Z軸についても、材料の取り付け高さを前機種よりも多めにとり、より3D加工をしやすくしました。
基板加工にも対応させました。CIP100は基板加工専用のモデルでしたが、専用であるがゆえに本体剛性はあまり高くなく、フライス加工にも制約がありました。そこでCLでは、オプションとして「基板加工アタッチメント」をご用意し、それを装着していただくことで基板加工を可能にしました。これにより、剛性の高いボディを土台とした高品質な基板加工が可能になる上に、フライスとしてもご利用いただくことができます。価格についても、CL100本体と基板加工アタッチメントの合計金額が、CIP100と大きく離れることなく実現することができました。
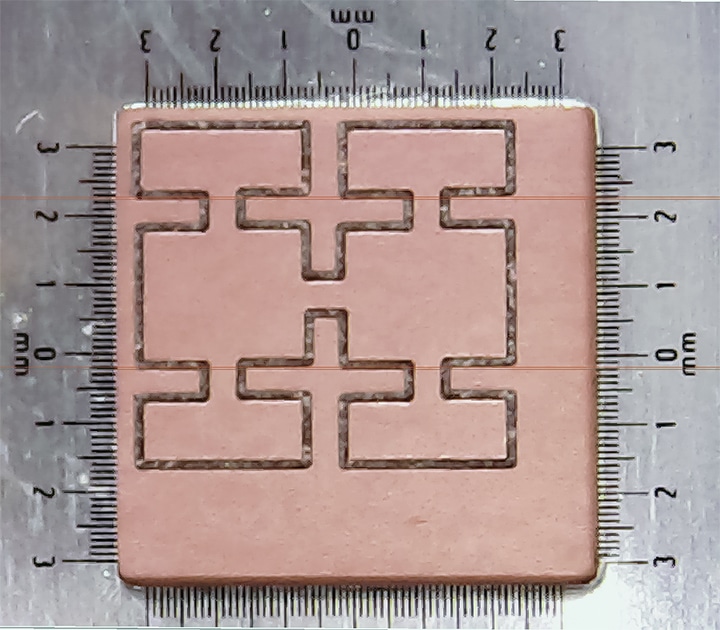
▲ CL100での基板加工。CIP100を上回る品質と精度で基板加工ができるようになった。
本体色は軽やかな印象を放つ純白にしました。SR100/200と同じ色ではあるのですが、塗装会社との連携を高め、より質の高い白となるよう徹底しました。白という色は手の抜けない色で、均一性を保つことがむずかしく、部品ごとに色合いがわずかに異なるといったことが発生しがちです。検査体制を強化し、全ての部品にわたって美しい白が均一に維持できるよう徹底しました。
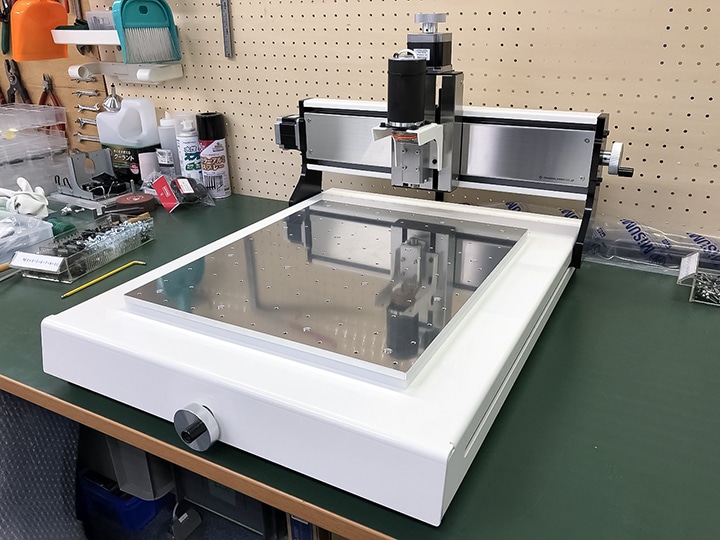
▲ 試作第5号機。最終製品と比べると、X軸カバーやサイドフレームの色が異なっているため違和感があるが、色を決めることは簡単なようで意外とむずかしく、試行錯誤を繰り返した。
このようにして美しい外観を実現しつつ、3つの機種を1つに統合し量産効果を高め、コストパフォーマンスを最大化するとともに、加工範囲を見直し、お客様の多様な創作スタイルに対応しました。そのほかにも、組み立てのしやすさ、メンテナンス性、操作性、加工精度について、これまでの経験を活かしながら、すべて前機種よりも上回るように設計しました。CLの開発をスタートしたのは2018年ですが、わたしたちはその時点で15年以上にわたる経験とノウハウを持っていました。CLには、それらのすべてを集約しました。
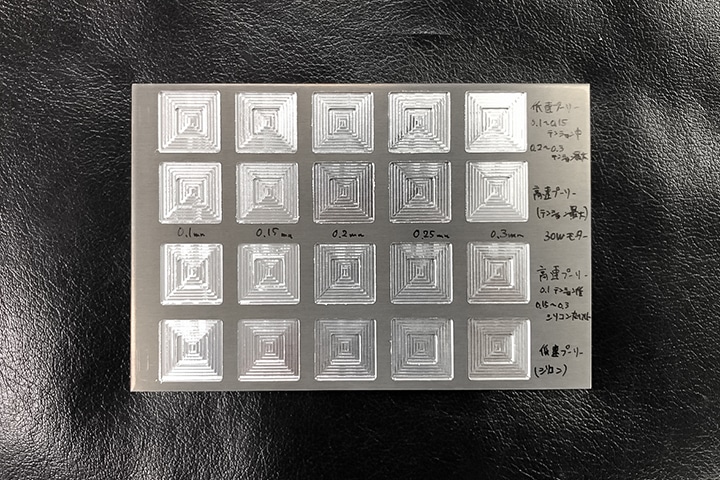
▲ 構成部品のどれか一つを変えただけで加工精度に影響があるため、設計変更のたびに精度を確認した。
【第五部】そしてKitMillは進化し続ける
KitMillは、2003年の誕生から21年以上が経ちます。振り返ってみますと、長い年月に渡りお客様がKitMillを受け入れてくださった理由は、いくつかあると思うのですが、その大きな理由の一つは、「気軽に使えること」ではないかと感じています。
一般的に工場で稼働する大型の工作機械は、高性能でパワフルな反面、それを扱うにはスキルや訓練が必要です。そのうえ高価であることから、万が一故障させてしまった場合の経済的負担と精神的負担はとても大きくなります。このため、気軽に利用することが難しいところがあります。
その点、KitMillは構造がシンプルでメンテナンスも容易ですから、万が一壊れても損失が最小限で済みます。コンパクトですから設置場所も選びません。こうした「気軽さ」が、お客様のニーズにマッチしたのだと思います。学校では、生徒さんたちが気軽に工作できる環境を求めていますし、企業においても、開発者たちは現場ではなく落ち着いた場所で研究できる環境を求めています。
アイデアは、ふとした瞬間に閃いては消えてゆく、儚い泡のようなものです。しかし、時にはそれが世界を大きく変えるほどの力を秘めていることがあります。だからこそ、アイデアをカタチに変える工作ツールには「気軽さ」が不可欠です。私たちは、高い性能を持ちながらも、気軽に使えるKitMillを提供し続けることで、アイデアを育て、世界を変えていくお手伝いをしていきます。さらなる進化と発展に向けて、挑戦の日々はこれからも続きます。
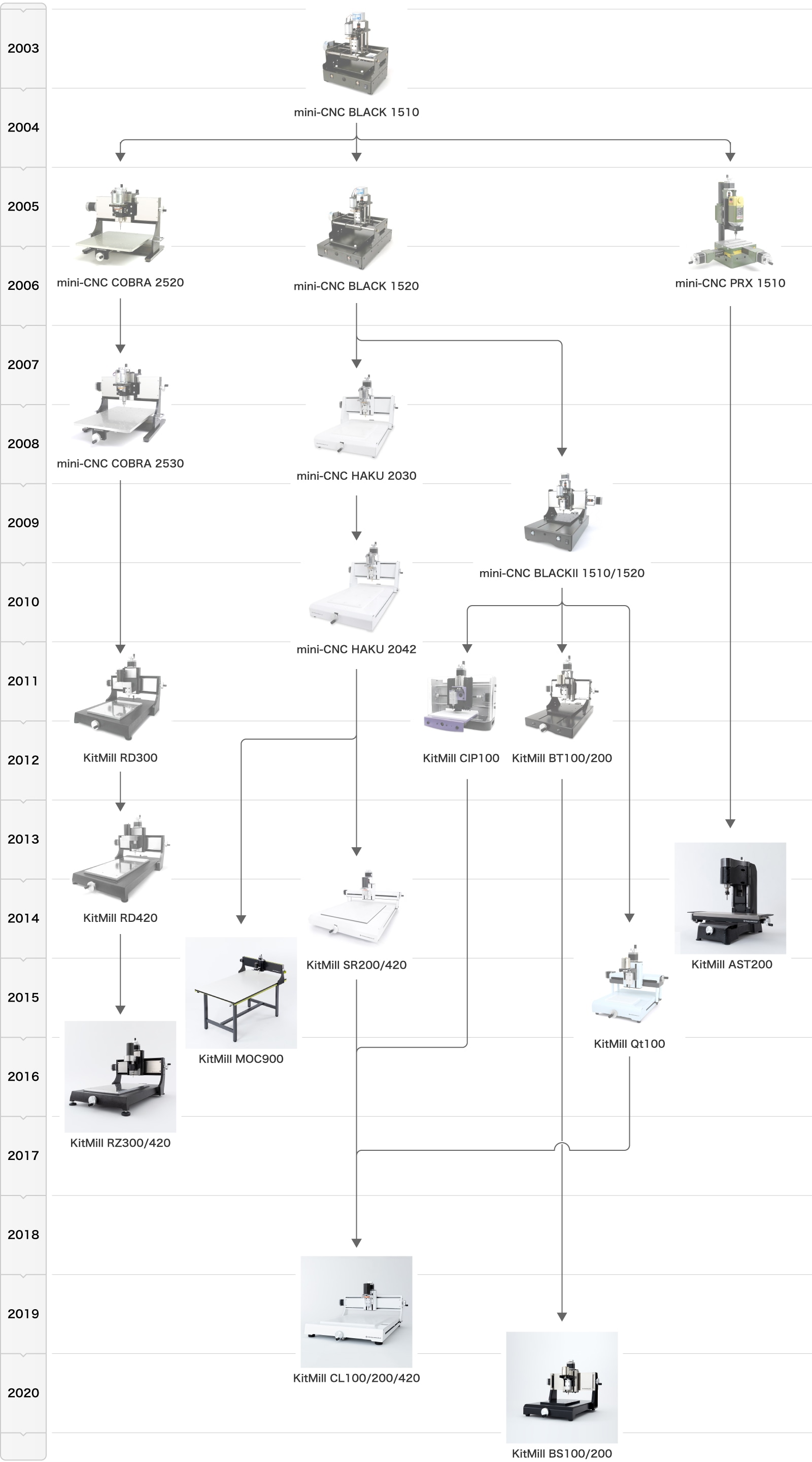
▲ KitMill年表。2003年の誕生以来、ここでは語り尽くせないほどたくさんの開発物語があります。